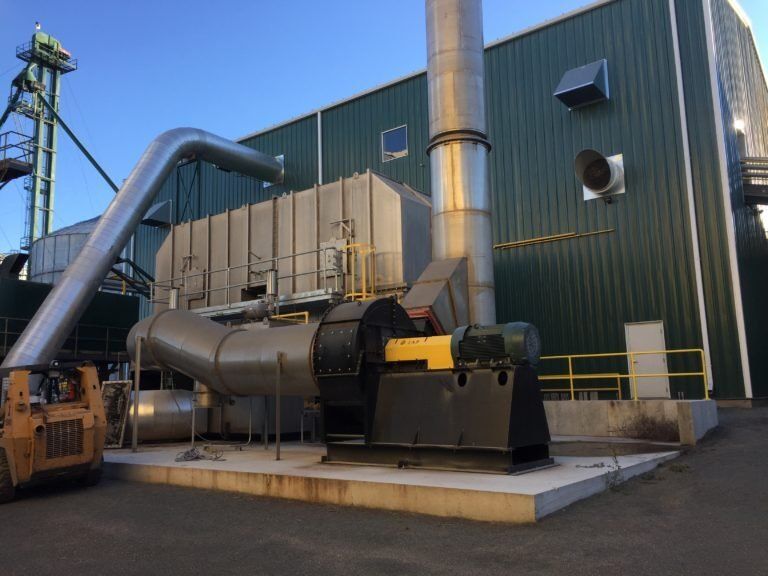
“What is a regenerative thermal oxidizer?” If your company produces emissions, you may have asked that question at one point in time. This is especially true if you were required to get one.
Whether or not you work for a company that has a regenerative thermal oxidizer (RTO), seeing one and understanding one are two different things.
In the above picture, you can see the average two-can RTO. Typically, it’s made of stainless steel, has a poppet valve system for directing the air and a tall exhaust stack. But how exactly does this process clean emissions? This article will attempt to explain that in a clear and simple manner.
HOW TO BEGIN THE REGENERATIVE THERMAL OXIDIZER DESIGN PROCESS:
To begin, you must understand the process air flow coming from the facility. What are the emissions composed of, and how much air flow will be pulled through the RTO? The answers to those questions allow for the initial design of the system to occur. Once we know how much air and the contents of it, we can figure out how big of a unit it will be. We can also learn how much media will be required to maintain temperatures at an efficient rate.
After all, that’s what makes an RTO such an efficient system. Not only is it known to break down harmful VOCs and HAPs at a rate of 97% or better, but it greatly reduces the amount of added gas the facility will need to supply to keep the temperature stable. This reduction of natural gas saves companies a vast amount of money every year in operating costs.
How does it do that? The media (generally, ceramic material) sits in the base of the two bottom chambers of the RTO. This media is able to store heat energy extremely well. So, the system is designed to utilize that heat energy and reverse the inlet air flow in intervals from one media chamber to the other. As the flow switches back and forth, the heat energy is transferred side to side with minimal loss after each switch. This keeps the entire upper chamber within the required temperature range necessary to get proper destruction efficiency.
The air flow also determines the size of the ductwork going into the system, as well as the size of the exhaust stack. If properly sized, the system will run more quietly. If it’s not sized correctly, loud howling sounds will be created by the air going through the duct.
THE BREAKDOWN:
Breaking all of this down, the emissions come out of the facility, into the RTO’s poppet valves, into the media chamber, reach temperature of destruction in the upper chamber and exhaust out of the stack.
If you’d like to see this all in action, visit our home page for an animated graphic of the process.
Contact Us Today!
For A Free Fabrication Quote